1. Finite element analysis (FEA)
Implant failure is common in the dental implant industry. FEA is becoming more used in implant dentistry, and it allows engineers/scientists to study bone and important implant properties. This process also helps them study Bone-implant interface as well as to understand how make improvements for design purposes in order to function correctly with natural movement within limits.
FEA operates on a computerized three-dimensional model base that has been extensively used to predict the characteristics of stress distribution in bone surrounding implants, which are influenced by both the implant dimensions and the bond formed between the bone and the implant.
By understanding the basic theory, method, application, and limitations of FEA in implant dentistry, the clinician will be better equipped to interpret results of FEA studies and expand these results to clinical situations.
2. Computer-aided design and technology
Implants and fabrication have had to undergo constant change and evolution. Today, since implants with more complex shape are used, CAD/CAM techniques are being implemented. This technique saves time and creates far more accuracy when creating the implants. CAD/CAM systems (computer-aided design / computer aided manufacturing) it’s been used for decades in restorative dentistry and has expanded its application to implant dentistry.
These systems consist of three components: 1) data capture using optical systems or laser scanning, 2) CAD for the design of the restoration, and 3) CAM to produce the restoration through the information generated by computer. CAD/CAM abutments present the advantages of being specific to each patient and providing a better fit than the rest of abutments, in addition to being much more tough as they employ materials such as titanium, alumina and zirconium.
In order to improve accuracy during implant placement we use stereolithography to manufacture CAD/CAM surgical templates. Using this method, minimally invasive surgery is performed without a flap, and the prosthesis is delivered, achieving immediate functional loading to the implants.
3. Micro casting
Using a metal melt which is cast into a micro structured mold, the micro casting technique enables the manufacture of small structures and complex geometrical details in the micrometer range. The advantages are relatively low cost and scalability from single items to large numbers of identical items.
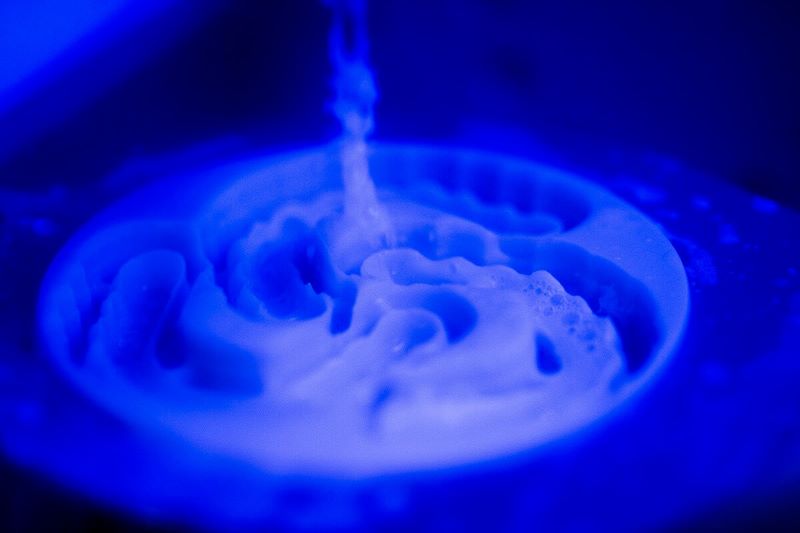
To obtain geometrical details in micrometer range, certain special manufacturing processes are required. Micro casting is one of the key technologies that enable the manufacturing of small structures in the micrometer range or of larger parts carrying micro-structures by using a metal melt, which is cast into a micro structured mold ( as mentioned above). Micro casting, is generally identified with the investment casting process, which is known as the lost-wax, lost-mold technique.
This process has the advantage of low wastage of raw materials. However, certain defects in the final product may result from the casting process, such as porosity due to poor filling, shrinkage, or dissolved gases; chemical segregation and hence non-uniform properties due to the physical chemistry of solidification; and contamination due to mold-casting interactions.
4. Nanotechnology-based implants
This approach may be the most fascinating of the dental implant options. A Nanotechnology approach requires new ways of manipulating matter on an atomic scale. Today, extensive research regarding techniques to produce nanotechnology-based implants are being researched and tested.
Nanotechnology-based procedures for dental implants consist of on surface roughness modification at the nano level to help protein absorption and cell adhesion, biomimetic calcium phosphate coatings, and the incorporation of growth factors for accelerating the bone healing process. Surfaces properties play a determinant role in biological interactions. In particular, the nanometer-sized roughness and the chemistry have a key role in the interactions of surfaces with proteins and cells.
These early interactions will in turn condition the late tissue integration. In this prospect, different methods have been reported for enhancing bone healing around metal implant. Modifying surface roughness has been shown to enhance the bone-to-implant contact and improve their clinical performance. Grit blasting, anodisation, acid etching,chemical grafting, and ionic implantation were the most commonly used methods for modifying surface roughness of metal implants.
Combinations of these techniques could be used such as acid etching after grit-blasting in order to eliminate the contamination by blasting residues on implant surfaces. This grit blasting residue may interfere with the osteointegration of the titanium dental implants. Nanostructured surfaces may control the differentiation pathways into specific lineages and ultimately direct the nature of peri-implant tissues. Despite an active research in dental implants, the ideal surface for predictive tissue integration remains a challenge.
In an ever changing world, dental implants along with the science and technology must keep up. The brains behind all of the changes are always on the lookout for new or better ways to create a better and longer lasting product for clients. It’s not only advancements in how implants are made, but what they are made of. Bio-materials have become essential for modern implants.
A suitable implant bio-material integrates into the body to perform a key function, minimizing negative immune responses. Keeping the primary Focus on dentistry, the use of dental implants for tooth replacement requires a balance between bodily response, mechanical structure and performance, and of course, aesthetics. A great amount of attention is drawn to optimizing surface modification processes and the additional use of coatings.
Alternatives and novel developments are addressed, providing potential implications of combining bio-materials to form novel composites that combine and coordinate the benefits of each material. It’s the in-depth science and research like this that will take dental implants into the future and create a better and even more reliable product for the client.
There is no, one correct answer when it comes to dental implant design and procedure, but know that as an industry, innovation is the key to growth. The Doctors and Scientist at Nuvia are always on the cusp of another breakthrough and are on the forefront of dental implant advancement.
Dental Implants are regarded as a far superior alternative compared to dentures and as more and more people obtain dental implants, we in the industry want to make sure the products last a lifetime.